Repareerbaarheid van keukenapparatuur en het aanbieden van reparatiediensten zijn voor ATAG heel gewoon. Manager Innovatie en Duurzaamheid Jan van Os laat zien hoe het bedrijf repareren in alle bedrijfsonderdelen heeft geïntegreerd.
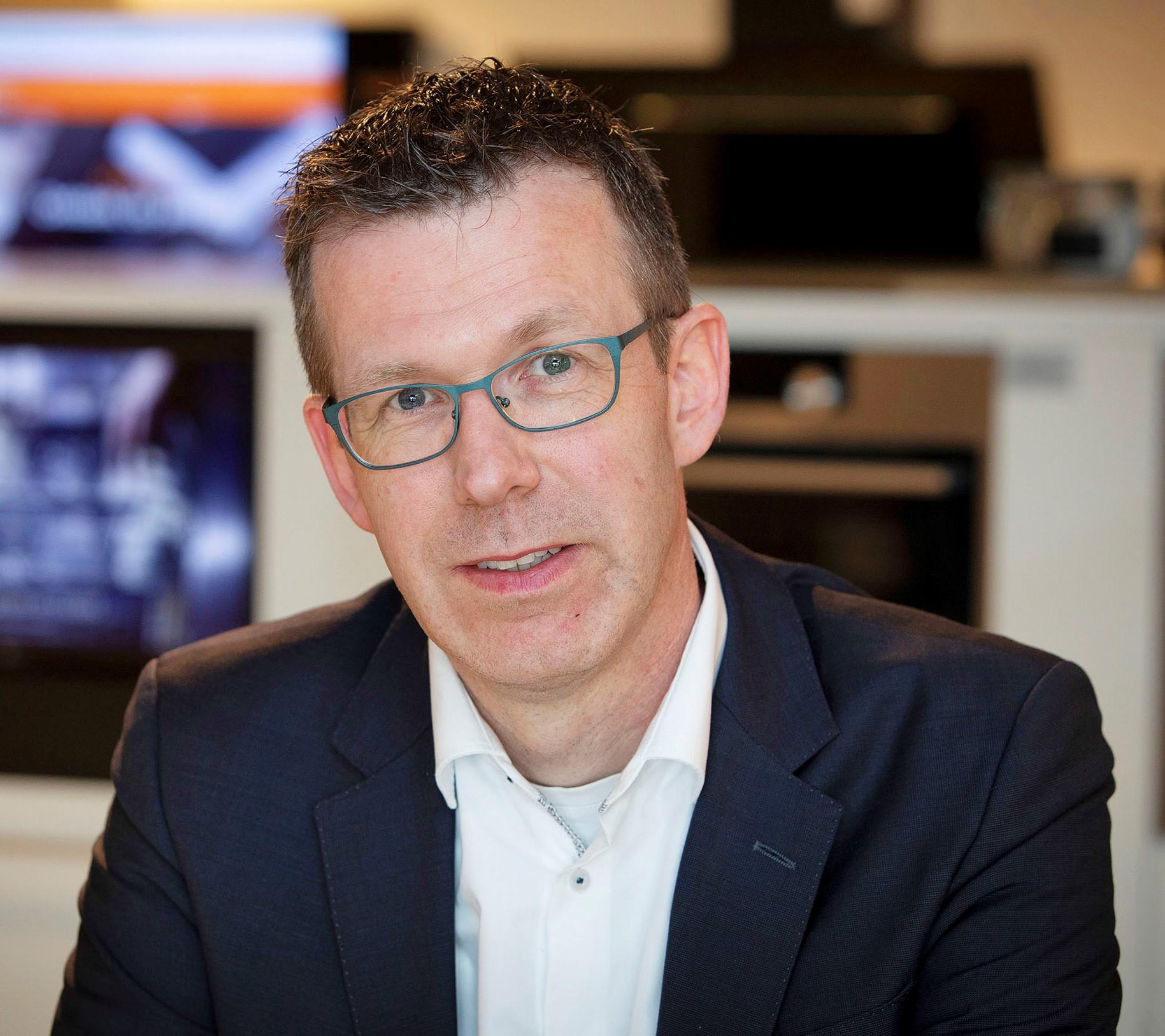
Productontwikkeling bij ATAG draait meestal om het verbeteren van een bestaande productlijn, bijvoorbeeld door het toevoegen van innovaties. Repareerbaarheid staat daarbij meteen vanaf het begin van productontwikkeling op de agenda: de afdeling aftersales wordt uitgenodigd voor feedback over de ervaringen van klanten met de oudere generatie producten. De sterke en zwakke punten van het bestaande product worden vervolgens meegenomen in het ontwerpproces voor het nieuwe product.
‘Ons bedrijfsbeleid is dat de meeste defecten binnen dertig minuten verholpen moeten kunnen worden’, zegt Van Os. ‘De ontwerprichtlijn is daarom dat producten eenvoudig gedemonteerd en gerepareerd moeten kunnen worden. In houten werkbladen geplaatste producten zijn bijvoorbeeld zo ontworpen dat ze vanaf de bovenkant te openen zijn, in plaats van dat toegang tot de elektronica via de onderkant loopt waarvoor je alle lades zou moeten verwijderen.’ Er zit een financiële reden achter deze aanpak. ATAG biedt een thuisreparatie service omdat hun apparaten meestal te groot zijn om naar een serviceprovider te brengen of per post naar de klant te sturen. Gemakkelijke toegang maakt snelle reparatie mogelijk en verlaagt de bijbehorende arbeidskosten.
De meeste defecten moeten binnen dertig minuten te verhelpen zijn’
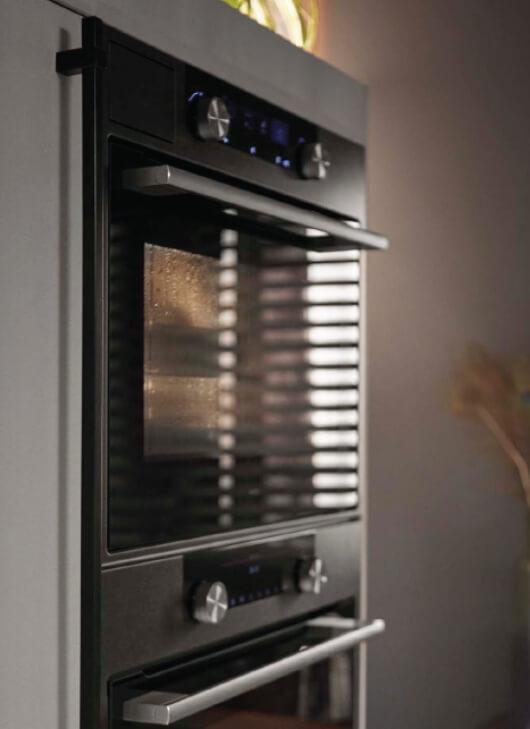
Servicemedewerkers met technische kennis
Naast de eenvoudige repareerbaarheid van de apparaten zelf zijn bij ATAG ook de interne bedrijfsprocessen ter ondersteuning van repareren in de loop der jaren geoptimaliseerd. ‘Onze servicemedewerkers beschikken over voldoende technische kennis om de problemen van de klant te kunnen vertalen naar de gereedschappen en onderdelen die nodig zijn om het probleem op te lossen’, zegt Van Os. ‘Ze worden vooraf in de gereedschapskist van de monteur geladen, zodat deze meteen op weg kan naar de klanten van die dag.’
Het bedrijf werkt ook aan de ontwikkeling van producten die een foutcode genereren en doorgeven, waardoor de afdeling aftersales, de servicemonteur, de reparateur en de consument op de hoogte worden gebracht van wat voor die oproep nodig zal zijn. Daarnaast traint een interne expert de in-house reparateurs in de producten en de organisatorische processen. ‘We willen voorkomen dat een monteur geen oplossing kan bedenken als hij in het veld is.’
We willen voorkomen dat een monteur geen oplossing kan bedenken als hij in het veld is’
Van database tot FaceTime
Om repareren en het vinden van technische oplossingen verder te vergemakkelijken, maakt ATAG gebruik van een intern databasesysteem. Van Os: ‘Technische bulletins beschrijven problemen en oplossingen voor een bepaalde productlijn, en deze worden met alle monteurs gedeeld. Als dat nodig is kunnen externe monteurs die we inhuren ook toegang tot deze database krijgen. Daarnaast gebruiken we moderne communicatiemiddelen – zoals FaceTime en andere visuele middelen – om verdere hulp te bieden bij het oplossen van een probleem.’
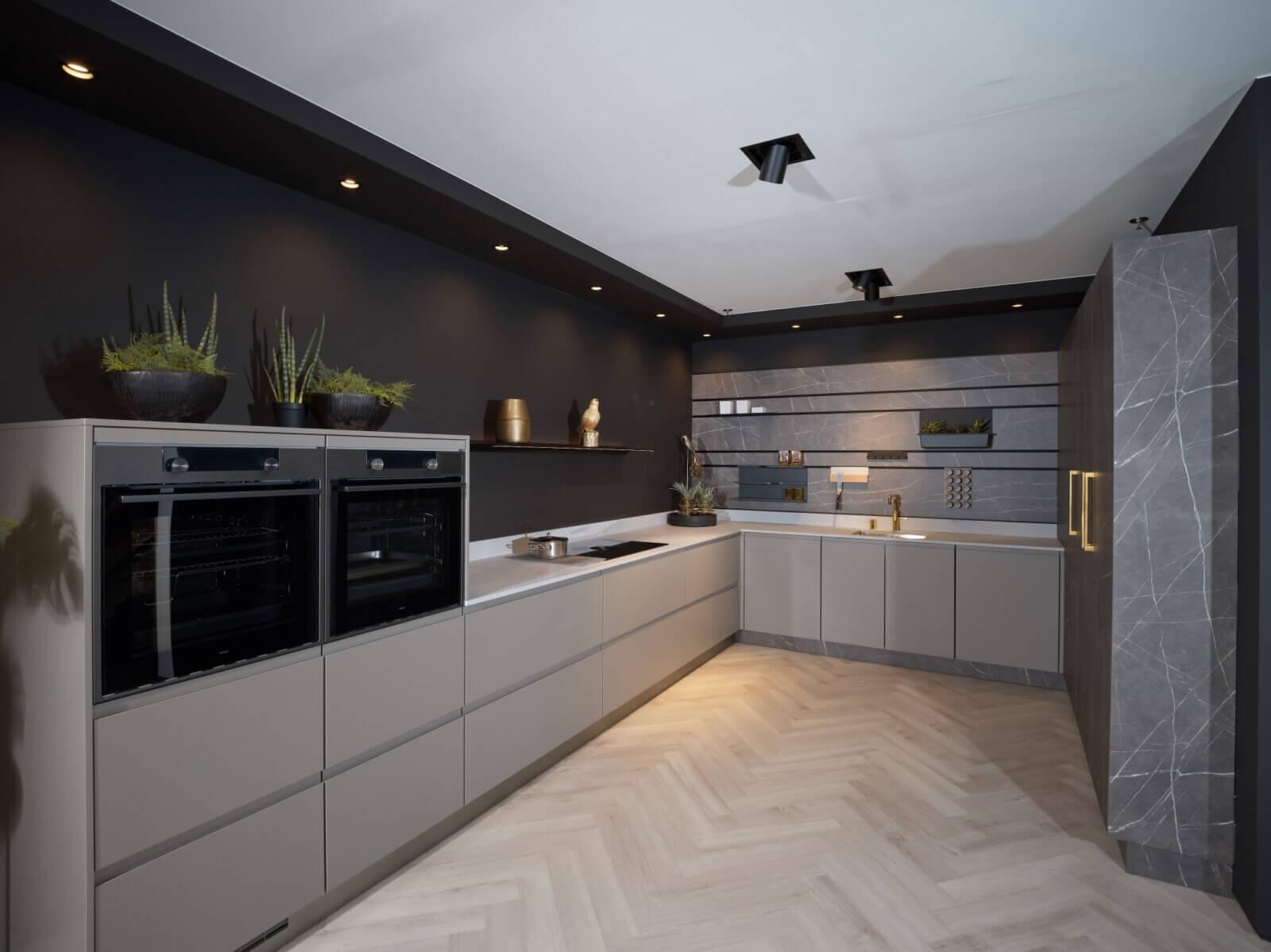
Reserveonderdelen: opslaan of 3D-printen?
ATAG biedt tot tien jaar garantie op hun producten en dit proberen ze te verlengen naar vijftien jaar. Om de beschikbaarheid van reserveonderdelen gedurende deze lange periode te waarborgen, sluit het bedrijf langetermijncontracten af met leveranciers. ‘We beschikken over een groot gebouw voor de opslag van serviceonderdelen. Toch zijn componenten soms niet op voorraad en is er een wachttijd van twee tot drie weken’, zegt hij. ‘Dat is frustrerend, want dan moeten we misschien toch overgaan tot vervanging in plaats van reparatie. We onderzoeken de mogelijkheden van 3D-printen als methode om beschikbaarheid op de lange termijn te garanderen en om de hiervoor extra benodigde opslagruimte te beperken.’
Soms zijn componenten niet op voorraad en is er een wachttijd. Dat is frustrerend’
Van Os is ook voorstander van een reparatie-index die consumenten voorlicht over de repareerbaarheid van een product. ‘Dit kan extra inspanningen van de fabrikant vergen, maar het vergroot ook de transparantie over de kosten van het product’, zegt hij. ‘Het kan de consument ertoe aanzetten het duurdere, maar duurzamere en gemakkelijker te repareren product te kiezen. Dat is goed voor het merk.’
Jan van Os is innovatie- en duurzaamheidsmanager bij ATAG Nederland BV. Hij studeerde Industrieel Product Ontwerpen aan de Haagse Hogeschool en begon zijn loopbaan als product engineer bij ATAG.
Dit is een artikel uit de nieuwe white paper 'Reparatie in de Circulaire Economie: Europese wetgeving, productontwerp en verdienmodellen,' een gezamenlijke uitgave van het Leiden-Delft-Erasmus Centre for Sustainability en de faculteit Industrieel Ontwerpen, TU Delft.